CASE STUDY
Outdoor sport lighting unit
When a customer got in touch with us to help design and manufacture a range of sport flood light units that were to be used in sport grounds such as five-a-side football pitches, tennis courts and leisure centre outdoor grounds. The unit was to have flexible design for a quantity of LED light modules through to specific manufacturing features to prevent bees and other flying insects making it their new home!
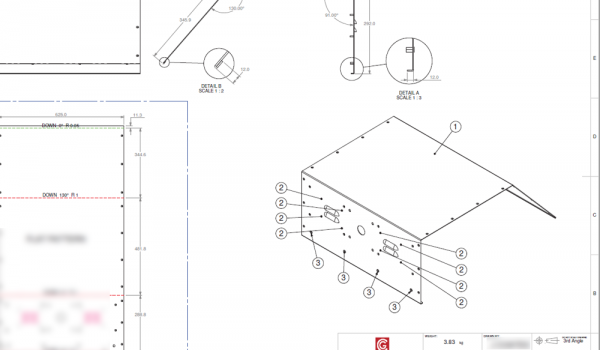
CAD design
Our in-house team of experienced CAD engineers sat with the client to gauge the full specification, considerations and manufacturing requirements the client would need. Then they drew up CAD drawings, including a 3D visualisation of the unit (including LED lights) for approval.
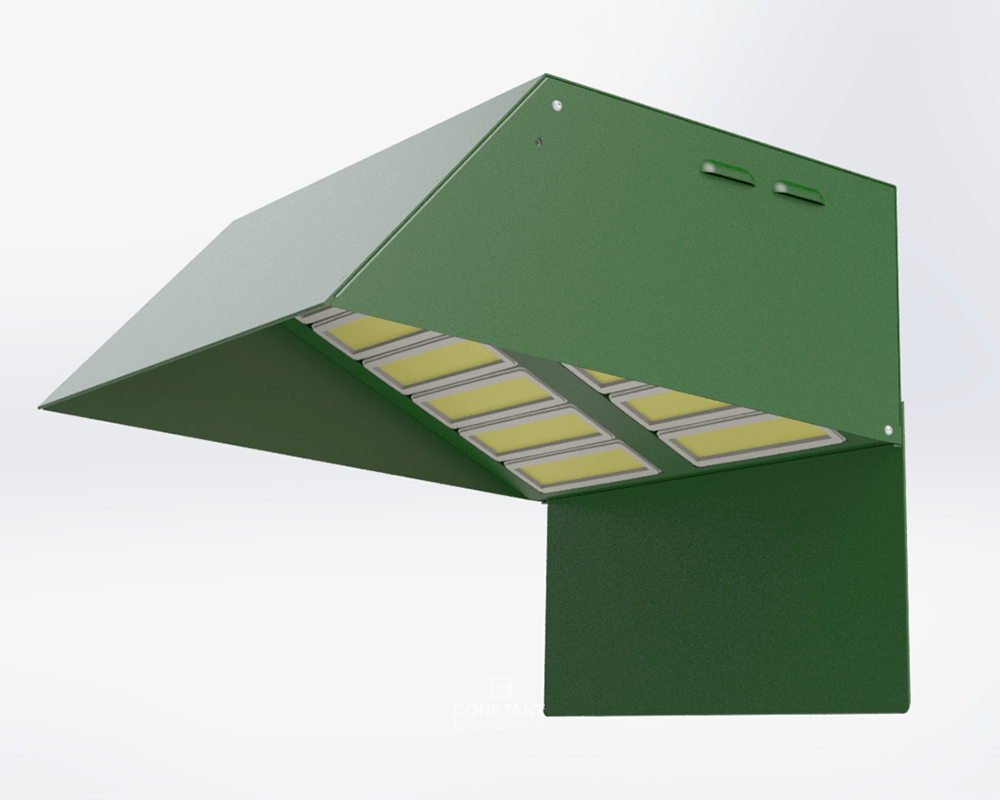
CNC punching
The unit is manufactured from 2mm thick aluminium. This helps the unit’s longevity with the aluminium anti-corrosive nature, as well as making it light enough for being fitted to a lighting pole or side of a building, and robust enough for its purpose. The TruPunch 3000 made light work of cutting the sheet metal.
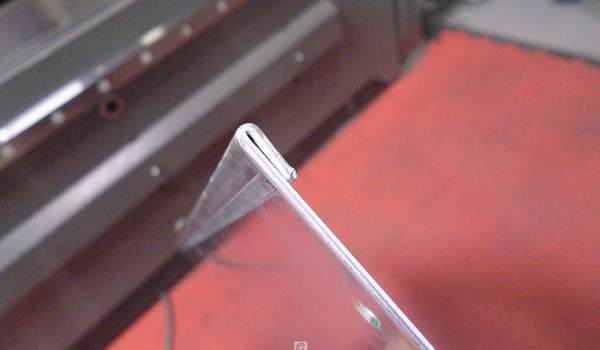
Bend and rivet
As the unit has exposed edges, unlike a cabinet, a safety edge was programmed into the design. This safety edge effectively folds the aluminium back on itself to create a smooth edge. The press brake team continued to bend the remaining parts, to create the distinct lighting angles of the floodlight enclosure. Once bent, the parts go to our experienced sheet metal workers and welders. The unit is rivetted instead of welded to reduce costs, speed up manufacture, and there is no aesthetic reasons for the unit to be welded.
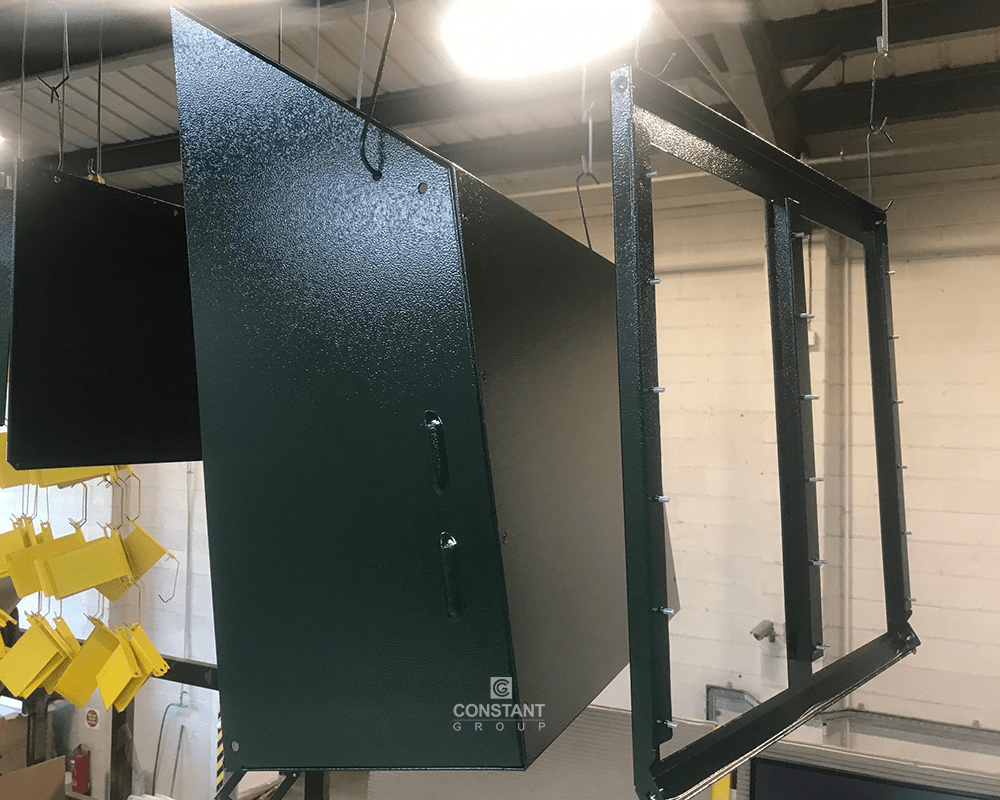
Powder coat
Adding a forest green powder coat finish to the unit adds another layer to the aluminium’s anti-corrosive benefits, as well as giving the lighting enclosure a layer of weather protection.
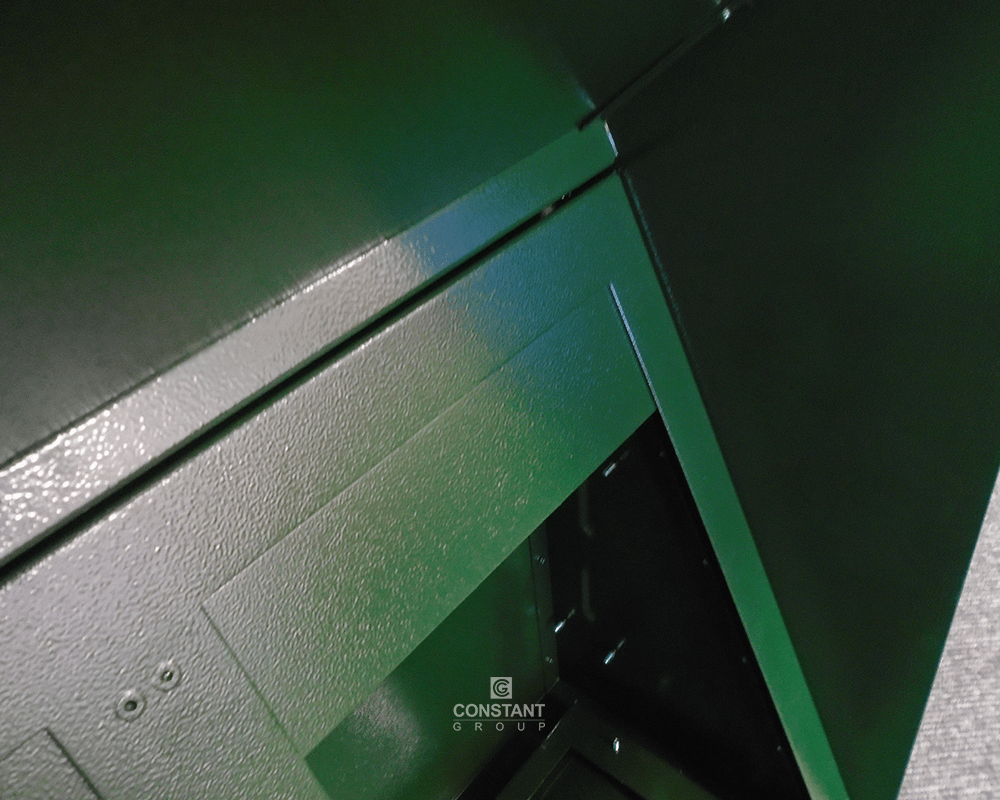
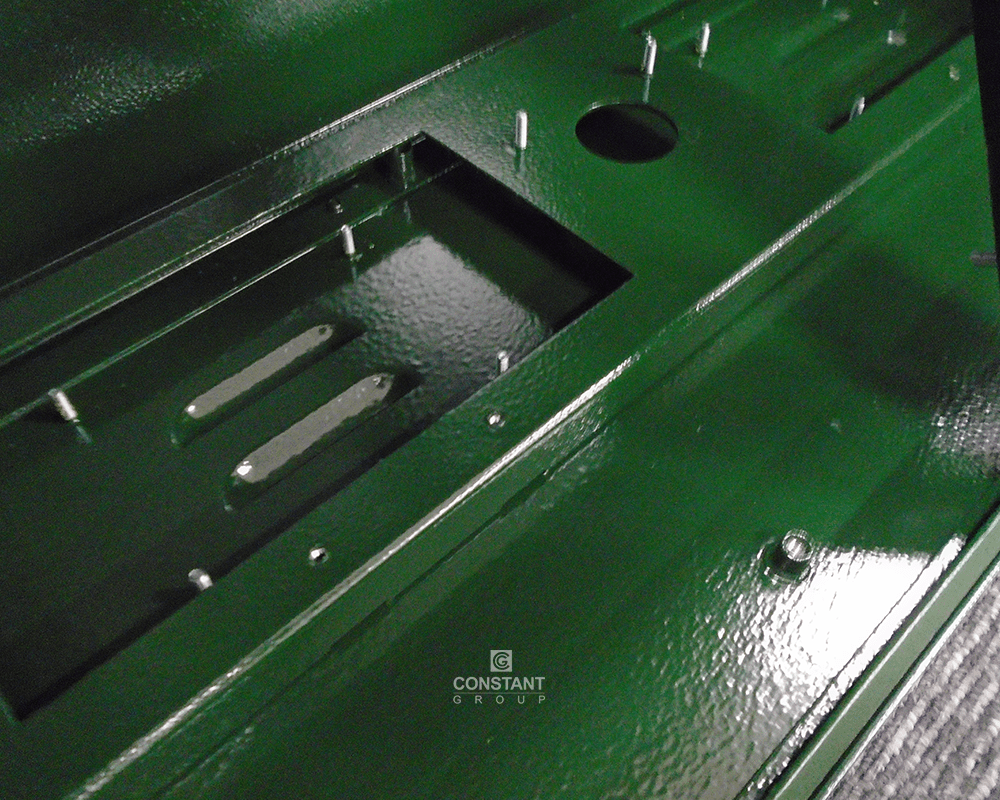
Assembly
The outdoor lighting unit has several design features which are noticeable when assembled. First is blank lighting plates (first photo). Not all installations will require the full 6 x 2 sets of LED lights, so an easy to fit blanking plate was required for when the light was being used in smaller areas with less light requirements.
The second feature is having the LED module on a rack system. It can be fixed in one of two positions so the direction of the LEDs can be tailored to the installation. In the second photo you can just see the blank hole for the fixings of the LED module to go into position.
Furthermore, it had to be bug proof! With the lighting units being installed outside, often in green-areas preventing bees and insects getting inside the lighting unit was key. So, no gap exposed to the insects could be more than 2mm wide. As seen in photo 3, the exposes base plates are flush to the back plate.
Final product
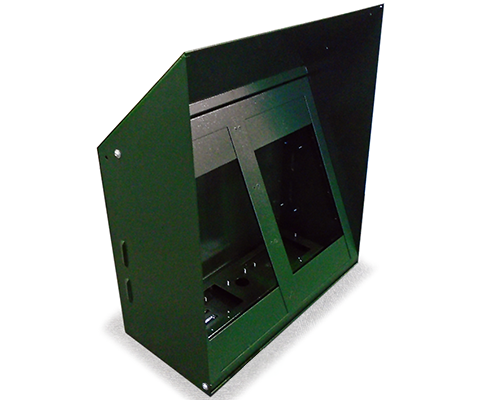