CASE STUDY
Mobile DOOH totem display
Customer
Destination
Leisure and travel
Industry
Advertising
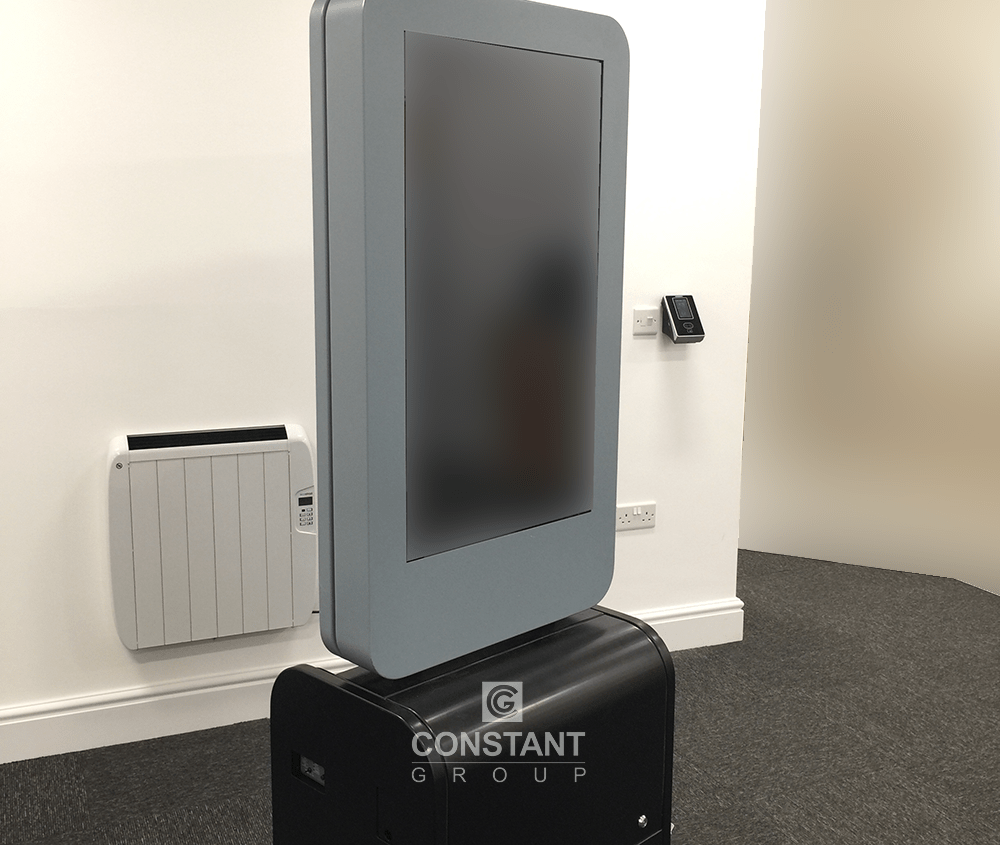
CAD design
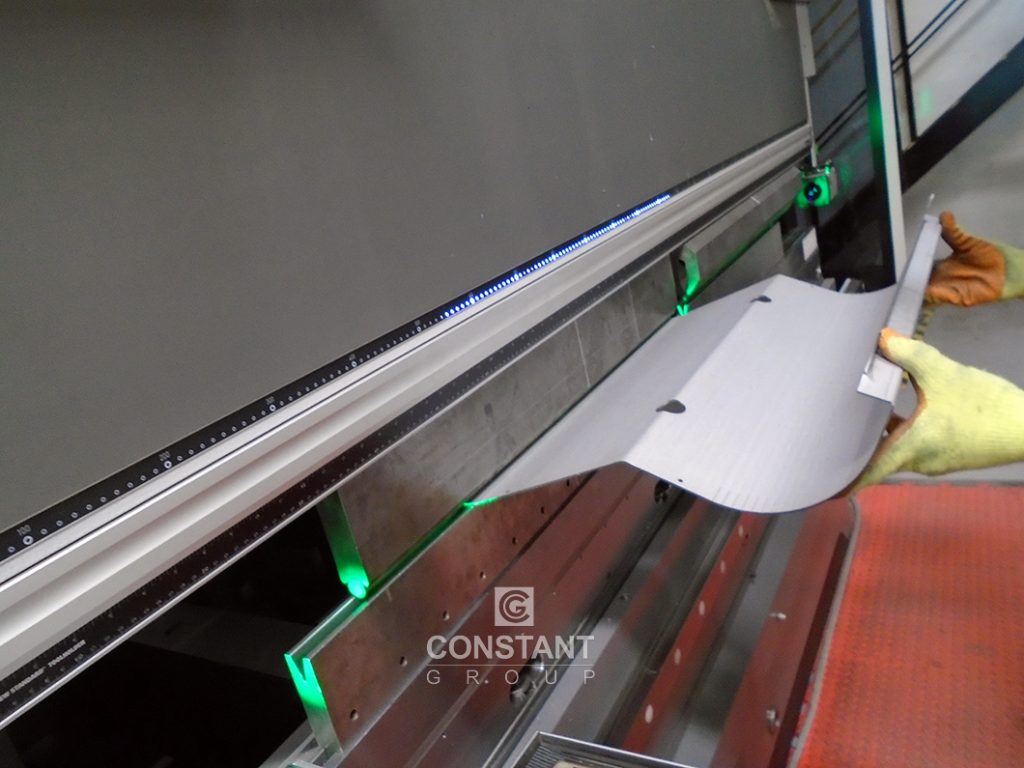
Laser cutting
Press brake
The CAD team programmed the press brake to do incremental bends in the metal work, to give the illusion of a curved front. A small bend every centimetre creates the desired effect, while keeping production lean (and costs down for the customer) by not involving exceptionally large traditional rollers to create the same radius bend.
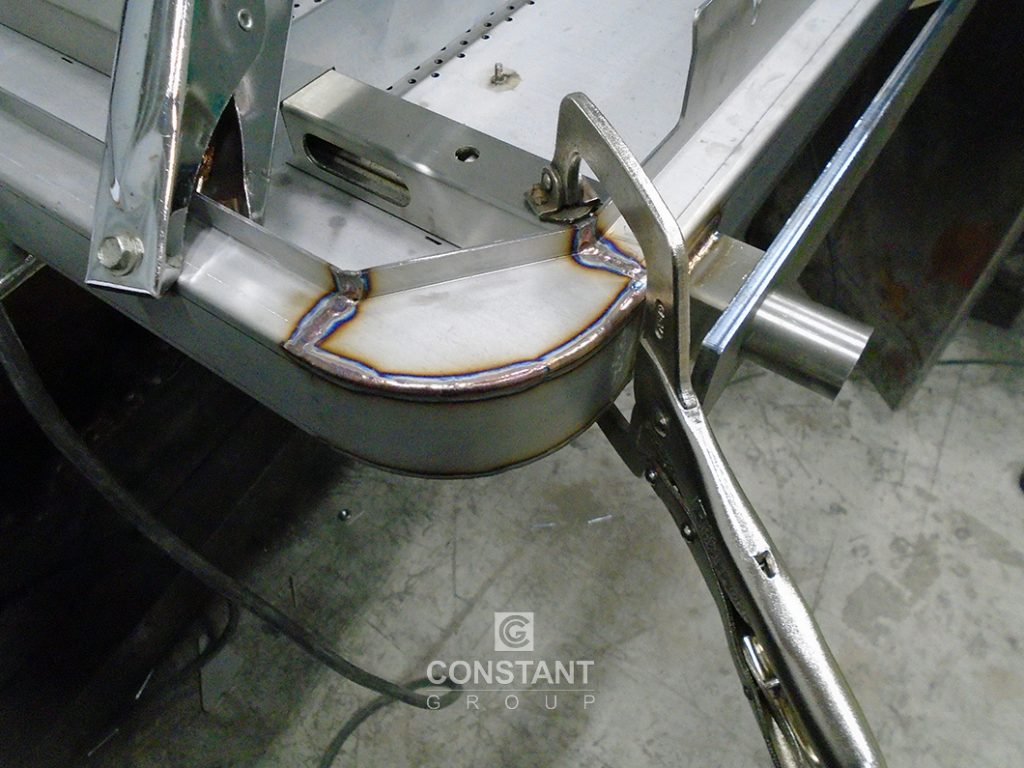
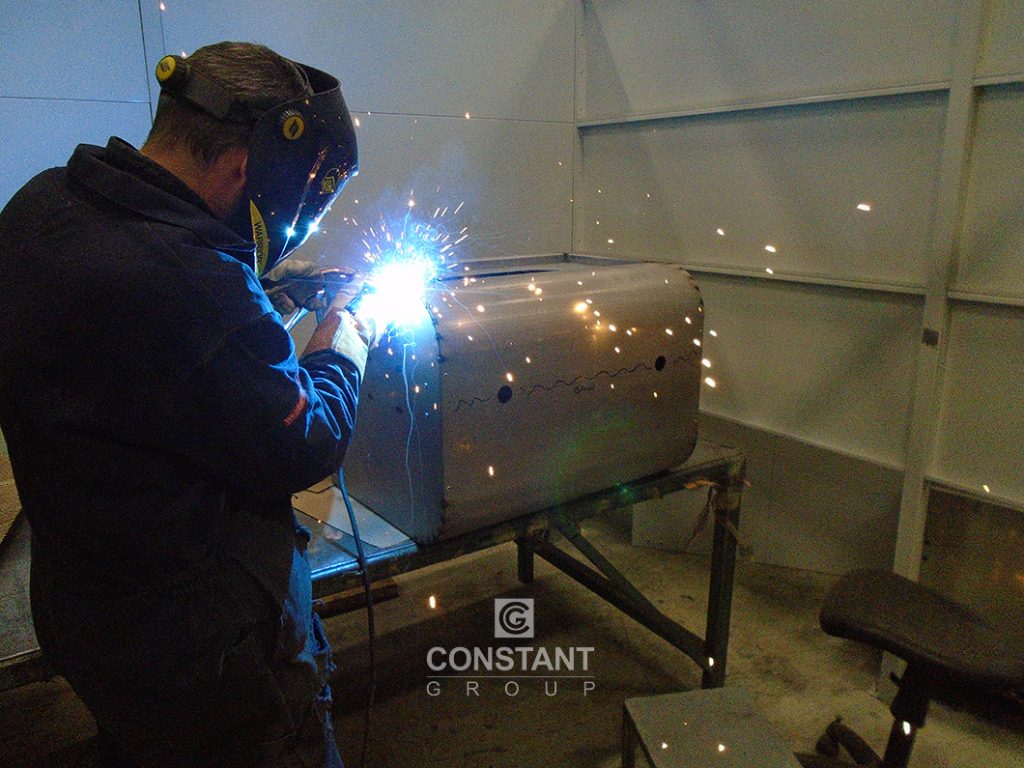
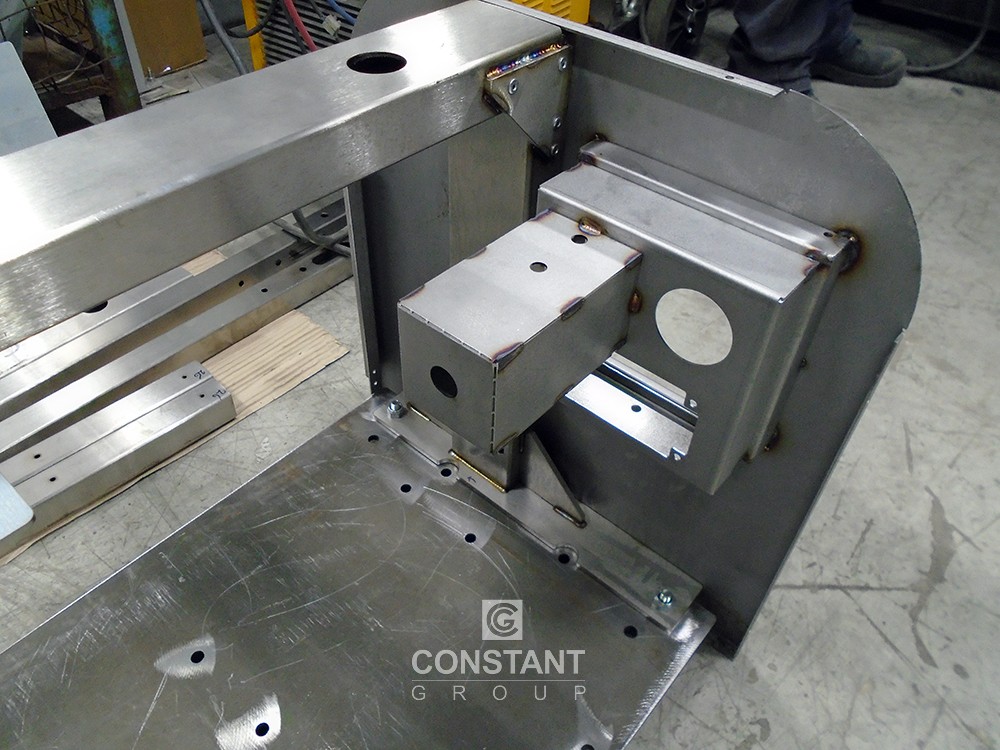

Welding
The first part of fabrication was using our Pemsertter, which auto-inserts the threaded studs into the metalwork. Once the studs were in place, the welding team got to work. Systematically the welder pieced the mobile totem together using guide castellation marks from the CAD engineer’s design and drawings to help align and fit pieces together. The mobile totem was pieced together using a combination of MIG, TIG and Spot welding due to the varied parts and fittings within the unit. The team then constructed the unit before it headed to powder coating. This allows for the CAD engineers and welders to assess any changes that may need to be done, and also double check it fits together.
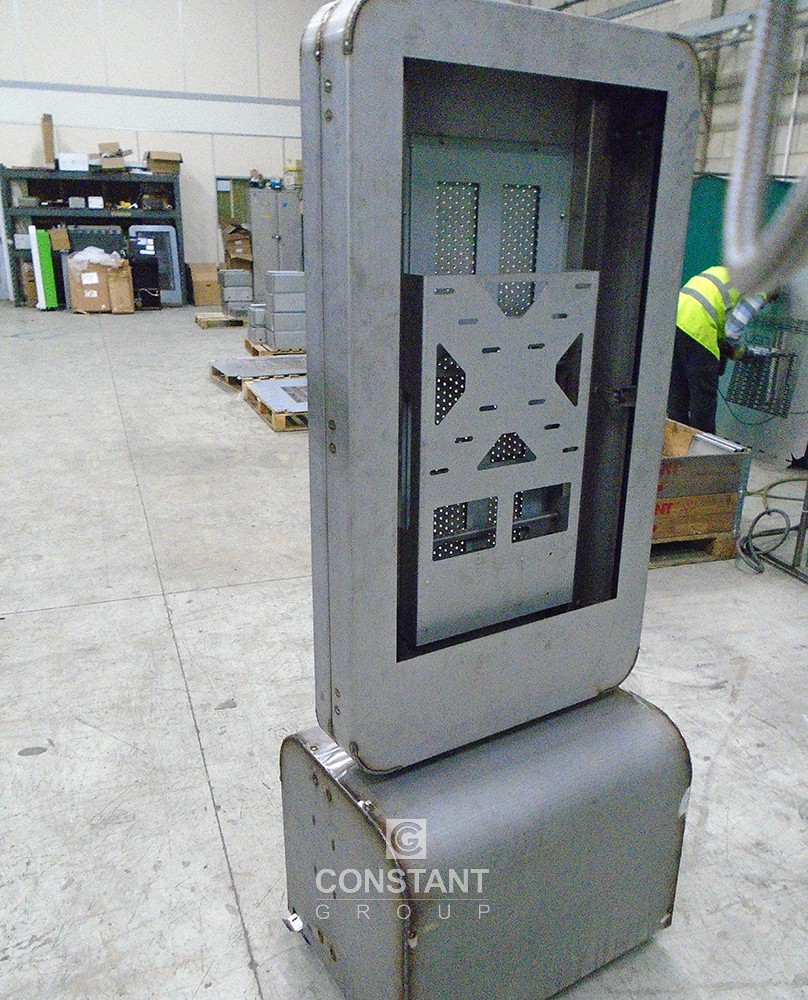
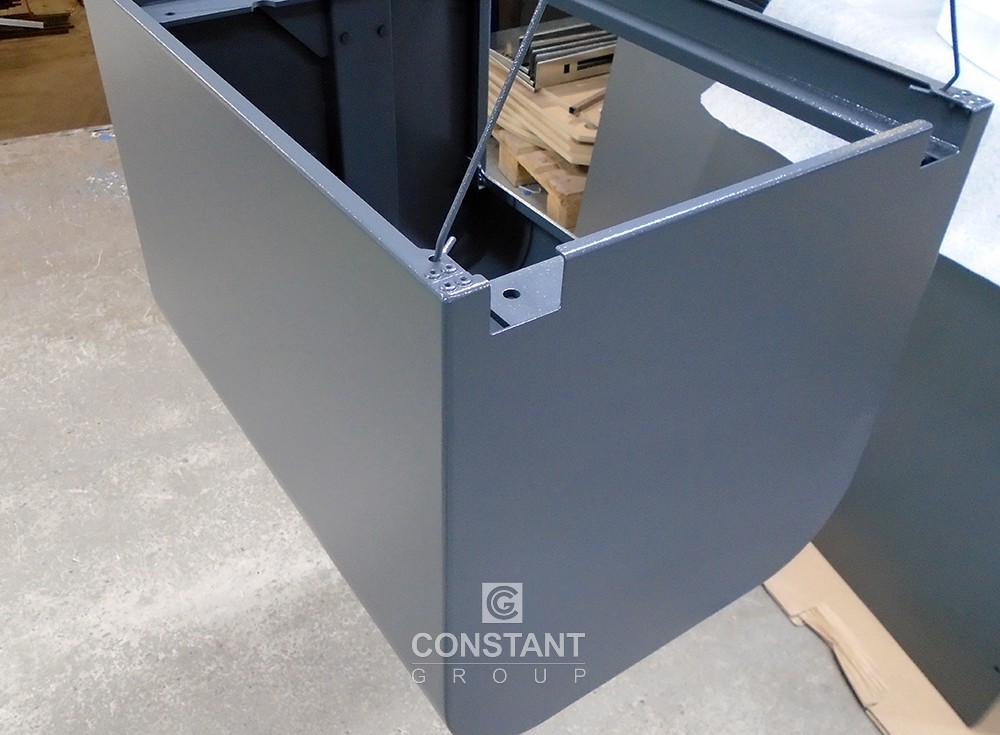
Powder coat
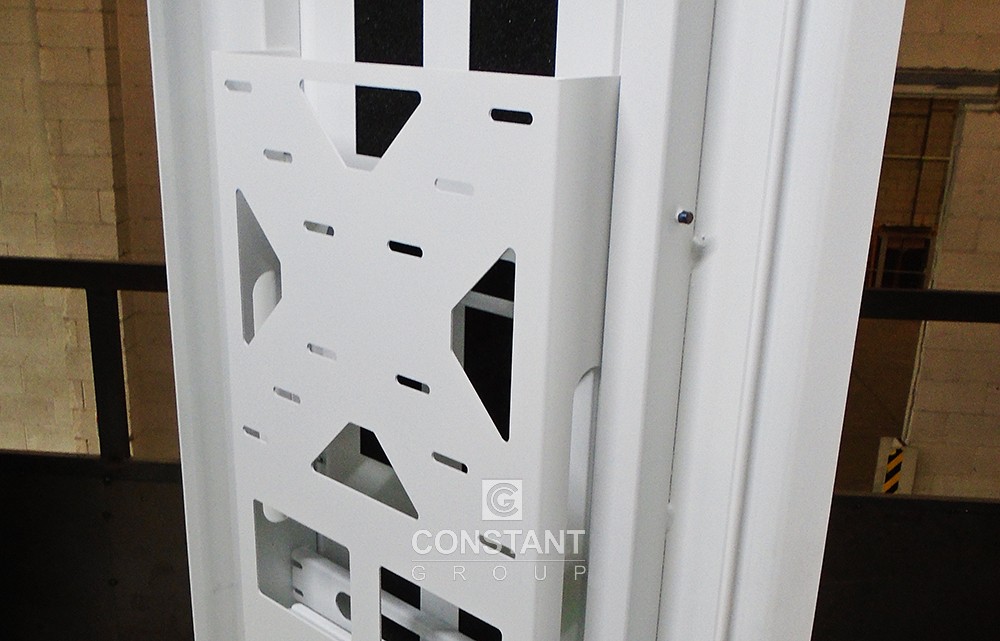
Assembly
The large assembly stage involved two members per unit, to fit all the bolts, foam sealing and combine the parts together. The assembly department fit all the monitor screen’s hooks and brackets into the inside, which allows for a variety of makes and models of TV screens to be installed into the unit with a large X vesa plate design. Again, making the unit more flexible and future proof for the customer. The back panel was designed with a few hundred vent holes, keeping the hardware inside at the correct temperature.
Final product
The finished mobile battery totem display stands at an impressive 6 foot in height, and 137kg in weight (without the equipment inside). It was tested to make sure it doesn’t topple over when the battery, screen and tech inside are installed. The bottom base unit has locking castors, removable plates for access to the battery and technology/wires, and a cubby hole for the charging cable to reel in/out. A clever design by the CAD team allows the cabinet to lock together, without the need for a key.
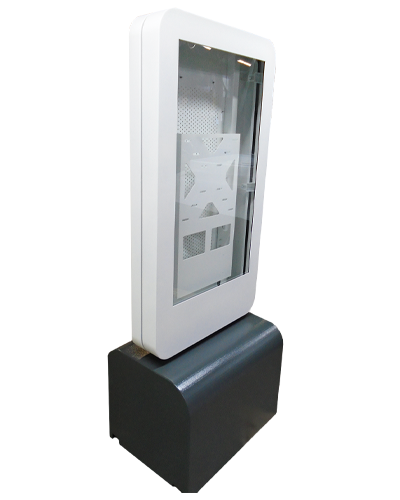