CASE STUDY
Digital out of home (DOOH) display
Advertising and display companies for years have been innovating their ways to communicate and engage with people when they’re in a queue, waiting for a train, or simply passing by a shop window. Digital Out Of Home (DOOH) displays are becoming more common place, with recent additions in service stations, cinemas and bus stops to name but a few locations. We’re delighted to work with a client on a revamped 43″ large scale DOOH display in totem format to be used in cinema complexes.
Customer
DOOH display solutions company
Destination
Cinema complexes
Industry
CAD design
As this was a re-development of an existing totem display, the CAD team worked from the customer drawings, as well as reverse engineering an existing sample. We discussed with the client any improvements they required, and the CAD team got to work. The final design incorporates revisions to every element of the design which ultimately lead to a leaner production reducing lead times and costs for the customer.
The CAD team accounted for swifter manufacture by utilising advances in our new Bystronic press brakes’ ability assisted by the offline programming which really helped visualise the number of bends on tis part before reaching the actual machine.
Laser cutting
This display totem was one of the last projects to be cut on our old Trumpf laser cutter, before our new Bystronic fibre laser cutter was installed and in full operation. The laser cutter makes short work of the various parts that make up the totem’s body and stand.
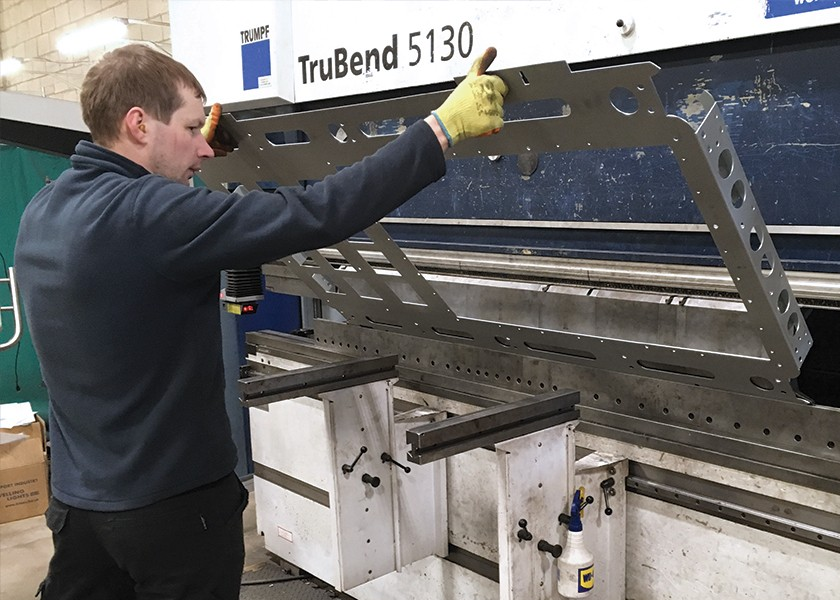
Press brake
The press brake team take each part of the body and base of the totem, and using the combination of the programming by the CAD engineers, and several years operators experience, they bend each into shape. You can see the various gaps in the metal work’s inner body.
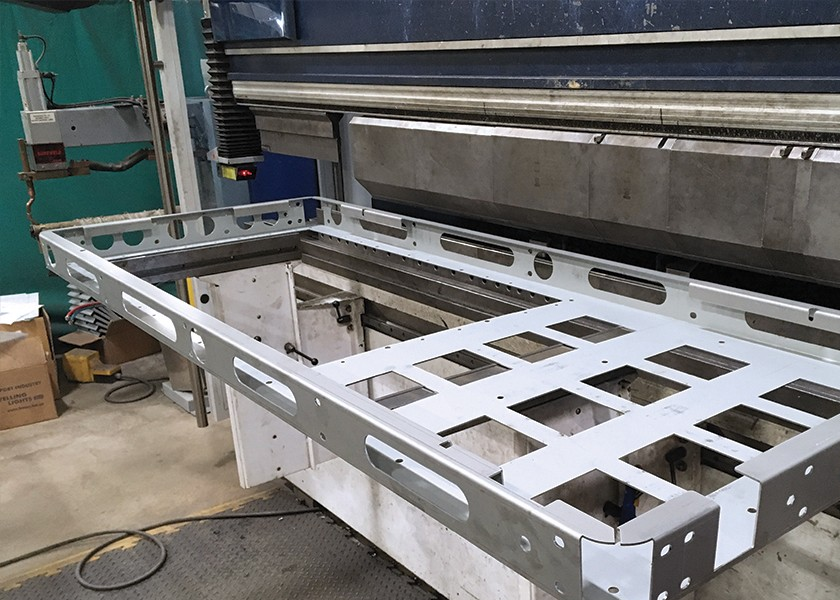
This isn’t for cabling or technology to be placed inside. It’s in fact to help make the items lighter, and make them easier to move into position, while maintaining structural strength by using specific ‘shapes’ in different parts of the unit’s design.
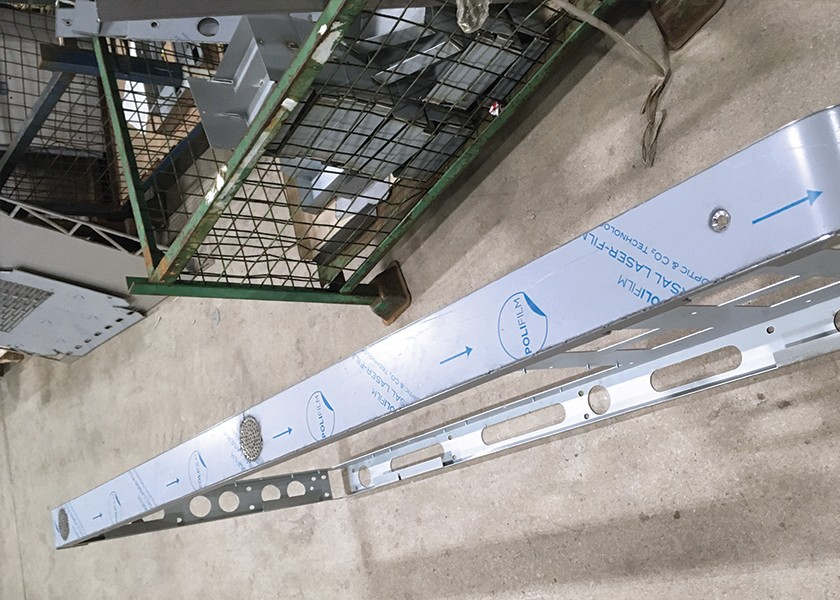
Fabrication
The totems (sometimes referred to as Kiosks), are made from a mixture of aluminium and stainless steel. The aluminium was to be powder coated white, with the stainless steel to be exposed. As a result, the stainless elements kept the protective film on as long as possible, which reduces the work the grinders and linishers have to do to ‘finish’ the metalwork.
The team built some simple bends into the metalwork, which saved fabrication time for the welders. Again, producing a swifter manufacture, and less handling time of the product.
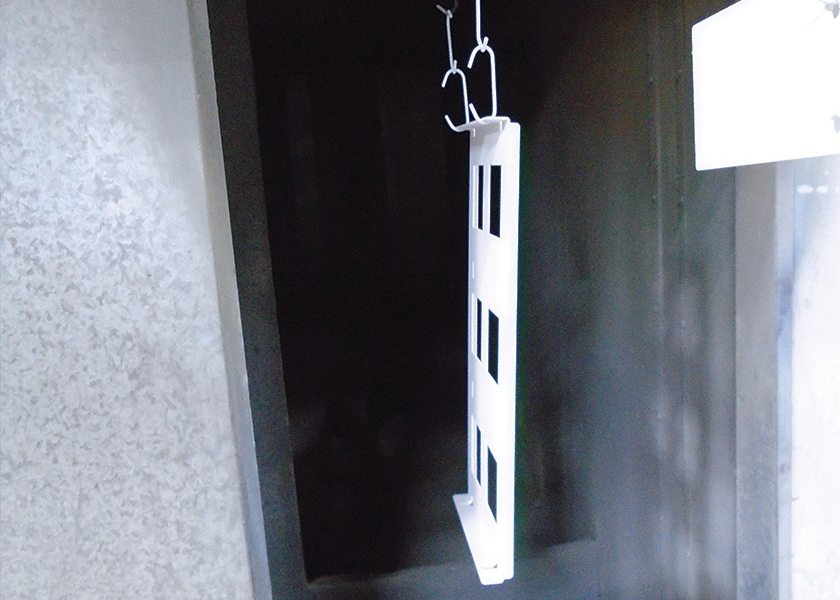
Powder coating
The aluminium parts went through the various stages of our on-site metal powder coating plant, to give the body of the totem a fine white textured appearance. The texture appearance/effect gives the metalwork some longevity and helps disguise any knocks, finger marks, or bumps it may get from foot-traffic when it’s deployed into a Cinema environment.
The combination of this powder coat finish, and the stainless rim was to emulate a modern mobile phone design/look and feel.
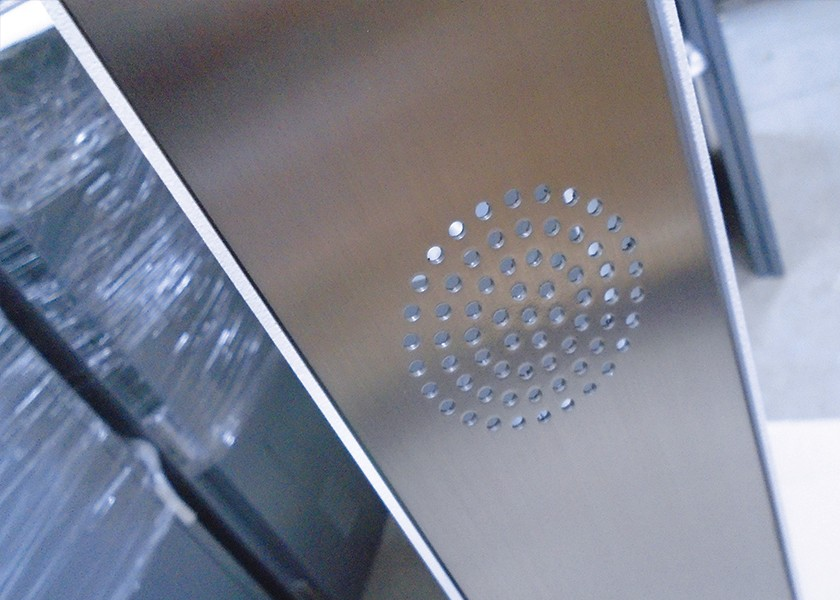
Assembly
Once powder coated, we fully assembled the totems with locks, neoprene seals and its foot plate. The totem was designed and manufactured to accommodate a large touch screen display inside, which meant the incorporation of various air vents to give maximum circulation of air, without compromising the look, feel and function of the totem display.
Final product
“We’re really pleased with the redesign of the totem. It stands over 6 foot in height and makes a distinctive and unmissable impression to the public. When you see the final totem with display screen installed, it certainly catches the eye and engages with the audience; which is exactly what the customer wanted!” – Matt Garlick, Managing Director, Constant

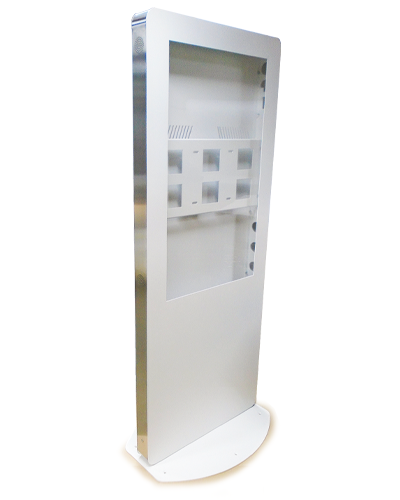