CASE STUDY
Counter POS display
We were approached to take a 3D visualisation render of a retail POS display by our client and create it into reality. The end display unit was made completely in-house at Constant from design to delivery.
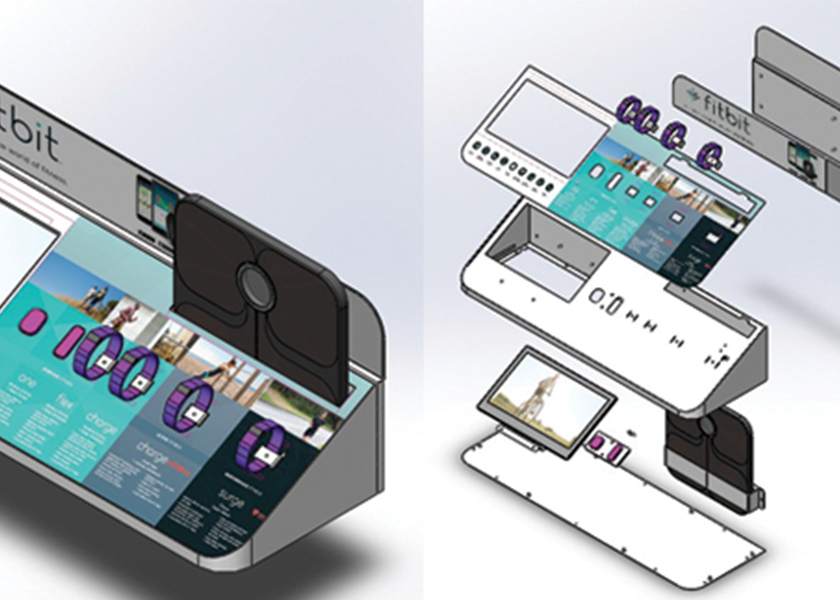
CAD design
The team of CAD engineers produced a complete visualisation of the POS retail display including the vinyl graphics and product units to be installed onto the display.
The unit is constructed from two sheets of mild steel. To give the best end result for the customer we used 2mm thick mild steel for some elements, and for small parts, and unseen parts, we used 1.5mm thick mild steel.
Punch and laser cut
The sheet metal is loaded onto our laser cutter for the main shapes to be formed. The middle photo is of the main body of the POS display, made from 1.5mm thick mild steel, with screw holes, product display sections, TV display cut-outs, and various shapes cut during the laser cutter stage to enable efficient fabrication and assembly.
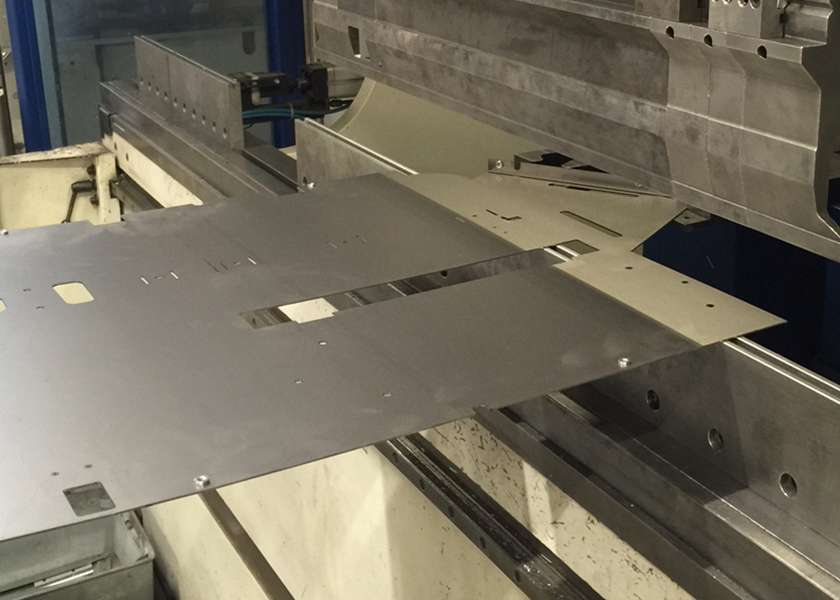
Press brake
Next the laser cut parts were taken to our suite of press brake machines to be bent into shape. They are programmed by our experienced supervisors who make sure that each bend aids a swift manufacture of the units.
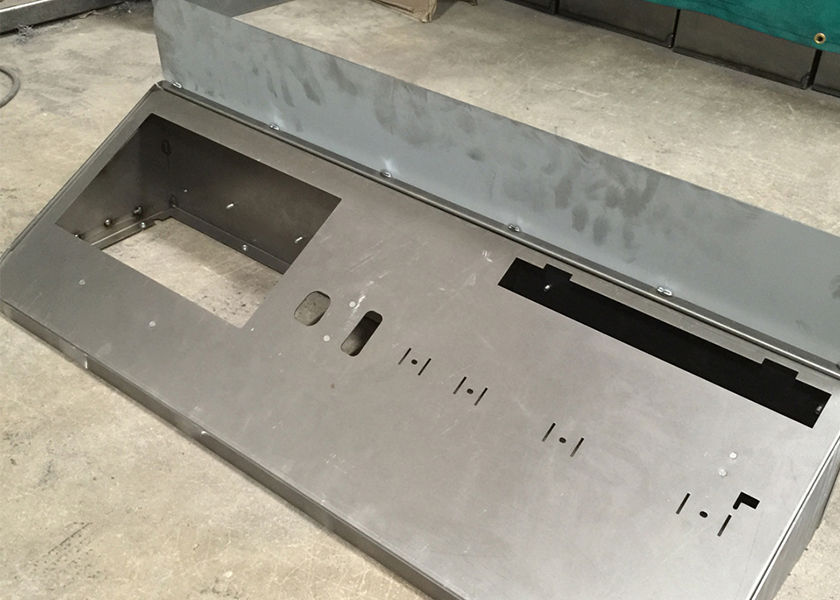
Welding
Once bent, the pieces are then taken to the team of welders who get to work forming the main base unit for the display. Then the team of linishers and grinders get to work on the units to make sure the entire display is smooth and free from blemishes.
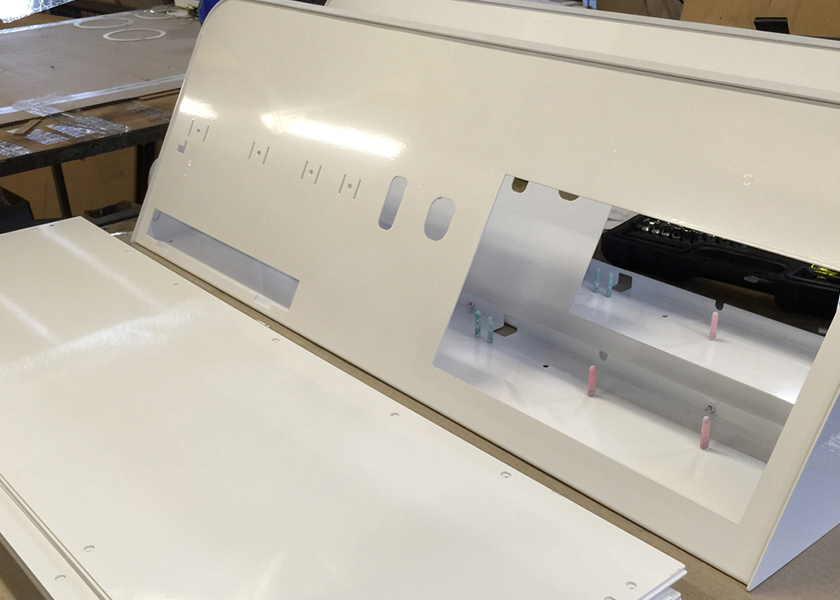
Powder coating
The smooth metal displays are now sent to the on-site powder coat plant to go through the pre-wash, coating
and curing stages of the finishing process. The curing oven process allows the powder coating mixture to fix onto the metal, producing a higher-quality finish without the need for traditional wet paints.
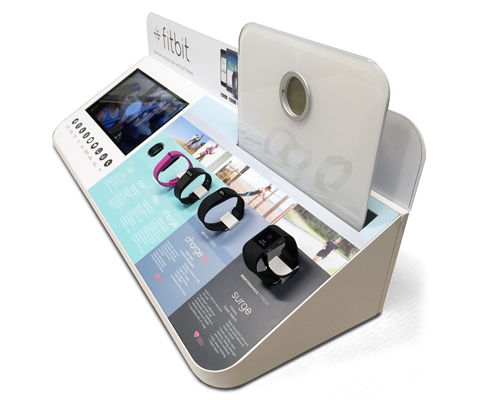
Assembly
When the units are cool, all the pieces are sent to the assembly department. Constant have a full assembly team in-house allowing for all stages of the production to be done under one roof. Once the white units are assembled, it was time to add all the display watches, flat panel screen, graphics and power cables. Then each POS display unit is packed securely into boxes ready for store delivery.
Final product
The completed units were well received by the retailers as they arrived ready to be displayed with secured cables connected and in place, and the units fitted perfectly into their store shelving. Our client was delighted with the finished quality, assembly and overall production of the units.
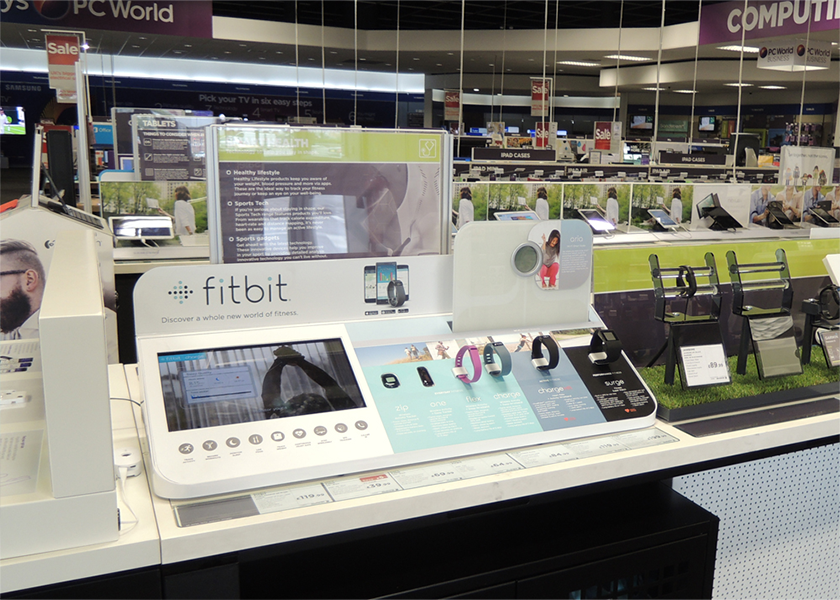